Projects
We understand what it takes to operate a successful galvanizing plant. Plant performance is determined from factors including, plant layout, equipment selection, technical knowledge & much more.
We understand these factors and ensure all elements are factored into the project and operational planning. We also provide on-going support to help ensure the plant achieves the objectives initially established for it.




Turn Key Solutions
KTE can offer a complete Turn-Key plant design solution. Every plant is unique and is specifically designed to meet the requirements of our clients. We can oversee the entire project or specific elements of it.
Backed with many years of operational experience in the galvanizing industry, KTE has the expertise to deliver the most efficient and effective solutions.
We work closely with our clients, keeping them updated and informed through every stage of the process – from concept, to start up and beyond.
Project Management
We can manage all or any part of the project. We utilise the latest systems to ensure we effectively manage the project from inception to completion and beyond.
- Complete project management service
- Client support with clear communication
- Documented project plans
- Project updates & meetings
- Site visits
- Liaising with external contractors and suppliers
Planning
The ultimate success of any project is determined by the meticulous planning process. Because our team has been involved in so many successful projects we have the knowledge and experience as the foundation for a successfully planned project.
- Product specifications
- Production throughput
- Plant sizing
- Materials handling requirements
- Environmental impact studies
- Utility analysis
Design
KTE offers a complete start to finish consultancy and design service. From site layout to complete materials handling. Utilising decades of experience and the latest design tools KTE provides the complete package:
- Latest 2D / 3D CAD software/ Finite Element Analysis
- Mechanical and electrical engineering
- Realtime materials handling simulation
- Handling and flow requirements
- Fully engineered drawings and documentation to Australian standards
Site Layout
Every site offers different opportunities and challenges. KTE has the team with the knowledge and experience to assess the best layout to minimise establishment costs whilst maximising operating efficiency and profitability.
- Custom plant design
- Initial conceptual layout
- 2 D and 3D plant layout with all equipment placed in position.
- Plans, elevations and section views
- Final detailed engineering drawings
Equipment
Selection and placement of equipment that will meet the long-term requirements of the client and which fit the initial budget requirements is a critical service provided by KTE.
KTE designs and installs a wide range of equipment according to operational requirements and budget. These plants may range from lower cost, manual systems, to semi-automated systems and through to state of the art fully automated high budget systems.
With energy demands, environmental factors and occupational health and safety standards playing an ever-increasing role, KTE’s knowledge of environmental requirements, galvanizing operations and available equipment to minimise energy consumption and emissions can ensure the designed outcome can meet the long-term needs of our clients.
In addition to designing into the plant the KTE manufactured Furnaces, Control Panels, Heat Exchangers and Metal Recyclers KTE have strong relationships with all of the industry’s well known, leading suppliers and can bring together all of the components required in a cohesive package.
Installation & Commissioning
- Industry experienced, fully trained and accredited installation teams
- Qualified gas & electrical technicians
- Functional acceptance testing of all equipment prior to delivery
- Pre commissioning checks
- Infinite tuning of combustion system for efficiency and production
- Complete combustion analysis
- Supporting documentation and manuals
Service, Support & Training
Routine service and maintenance
24/7 technical phone support
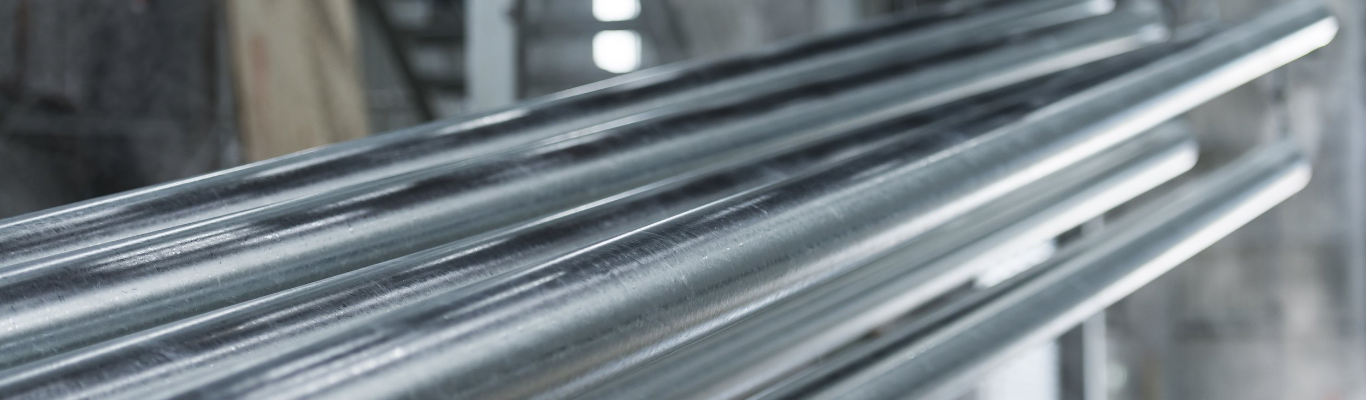
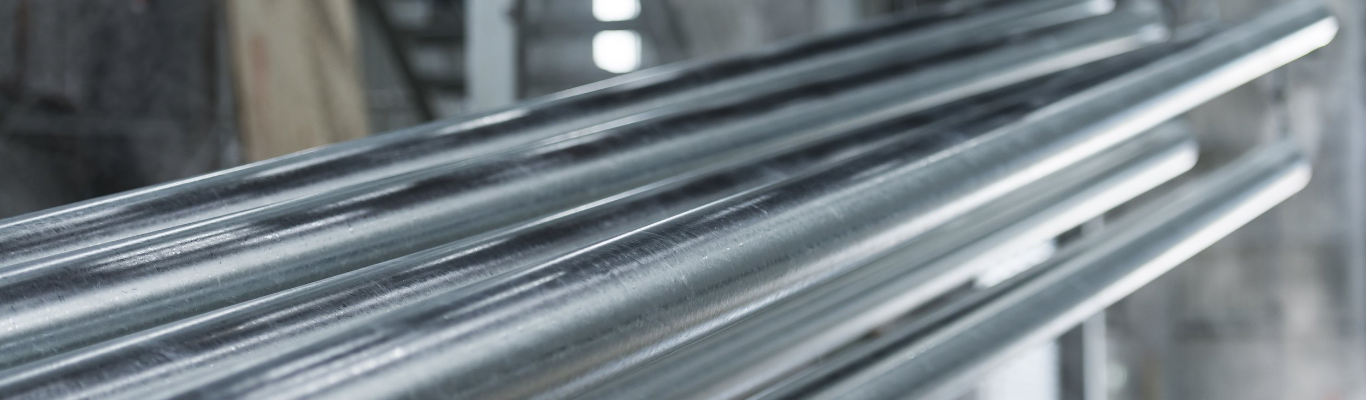